مرجل بخاري
المراجل البخاريةأو الغلايات boilers أو مولدات البخارsteam generators ـ وهي وعاء فلزي يتم فيه تسخين سائل معيّن حتى يتحوّل إلى بخار. ومعظم الغلايات تحوّل الماء إلى بخار يُستخدم لتدفئة المباني. ويتغير البخار من الصورة الغازية إلى الصورة السائلة عندما يستخدم في تدفئة حجرة أو مبنى، وبذلك يعطي حرارة أكثر نتيجة لذلك. وبعض أنظمة التدفئة التي تسمَّى الأنظمة الكهربائية المائية تستخدم الماء الساخن بدلاً من البخار. ومع ذلك فإن مصدر الحرارة في هذه الأنظمة مازال يعرف بالغلاية. ويستخدم البخار الناتج من الغلايات في التوربينات البخارية وتكرير الزيوت وتجفيف الورق. وتُسمَّى أحد أنواع هذه الغلايات، الغلاية ذات أنابيب الاحتراق، وتمرر فيها الغازات في أنابيب مُحاطة بالماء. ويستخدم هذا النوع من الغلايات في معظم القاطرات البخارية، وفي المصانع الصغيرة وأحيانًا لتدفئة المنازل. والنوع الثاني من الغلايات هو الغلاية ذات أنابيب الماء وفيها تمرَّر الغازات على أنابيب مليئة بالماء. وتتصل كل من نهايات أنابيب الماء بأوعية كبيرة الحجم تُسمَّى البراميل. وكل الغلايات ذات الضغط العالي والكبيرة الحجم تكون عادة من الغلايات ذات أنابيب الماء. وتتحمل الأنابيب الصغيرة في الغلاية ذات أنابيب الماء ضغطًا عاليًا بدرجة تفوق تحمل الأوعية الضخمة الخاصة بالغلاية ذات أنابيب الاحتراق.
يتجمّع البخار المتولّد في أنابيب الغلايات ذات أنابيب الماء عند الفتحة العلوية للبرميل. ويسير البخار بعد ذلك في مجموعة من الأنابيب تُسمى المحمصة. وتمر الغازات الساخنة على هذه الأنابيب المملوءة بالبخار، فتزداد درجة حرارة البخار. وتسمَّى عملية الجمع بين الغلاية والمحمصة مُولّد البخار.
بإمداد العديد من المصانع ومحطات الطاقة بالبخار الضروري للعمليات الإنتاجية تحت ضغط فائض، ويعدّ الموقد أو غرفة الاحتراق furnace أحد أهم أجزاء المرجل، وفيه تحرق كميات الوقود الضرورية، فتتحول طاقتها الكيميائية إلى طاقة حرارية. تنتقل الطاقة الحرارية من الغازات عبر الجدران المعدنية الفاصلة ما بين مسار غازات الاحتراق ومسار الماء والبخار اللذين يجري تسخينهما. ويطلق اسم مولدات البخار على المراجل للدلالة على العمليات والتجهيزات الأخرى الضرورية لإنتاج البخار، مثل إعداد الوقود والتغذية بالمياه والهواء وطرح نواتج الاحتراق، هذا فضلاً عن إطلاق الطاقة الحرارية وانتقالها إلى الماء لتوليد البخار.
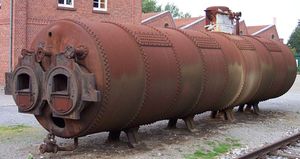
. . . . . . . . . . . . . . . . . . . . . . . . . . . . . . . . . . . . . . . . . . . . . . . . . . . . . . . . . . . . . . . . . . . . . . . . . . . . . . . . . . . . . . . . . . . . . . . . . . . . . . . . . . . . . . . . . . . . . . . . . . . . . . . . . . . . . . . . . . . . . . . . . . . . . . . . . . . . . . . . . . . . . . . .
لمحة تاريخية
ورد وصف المراجل أول مرة قديماً في كتابات هيرو Hero الإسكندراني نحو عام 130ق.م، وكانت أكبر قليلاً من لعب الأطفال. وفي عصر النهضة جرت عدة محاولات لإيجاد طرائق لاستخدام طاقة البخار، فكانت رسالة ماتيزيوس Mathesius في عام 1571. وفي عام 1679 أنشأ دنيس بابان Denis Papin مرجلاً محتوياً على صمام أمان، وتبعه آخرون. وفي عام 1796 ظهر مرجل جيمس وات James Watt، وبفضله ظهر اختراع ويليام بلاكي William Blakey الذي مثَّل أول مرجل أنابيب الماء water-tube boiler. وقد بدأ الاستخدام الصناعي للمراجل في أوائل القرن الثامن عشر نتيجة لنمو صناعة استخراج المعادن والفحم. وأخذت تصاميم المراجل أشكالاً بسيطة حتى منتصف القرن التاسع عشر، فكانت تصنع من النحاس في أول الأمر ثم من الحديد الصب. وسار تطوير المراجل لاحقاً في اتجاهين، أولهما احتواء مسار الغازات على عدد أكبر وأكبر من الأقنية، وهو ما أدى إلى ظهور مراجل أنابيب اللهب والغاز fire -tube boilers، وثانيهما زيادة عدد أقنية الماء والبخار (مراجل أنابيب الماء). إن زيادة سطح التبادل الحراري بزيادة عدد الأقنية أدى في الحالتين إلى زيادة سطح التبادل الحراري وزيادة الفعالية الاقتصادية للمرجل بزيادة المردود والإنتاجية، مع زيادة غير كبيرة في وزن المرجل، أي استهلاك المعدن.
في حالة مراجل أنابيب الغاز كانت إمكانات رفع ضغط البخار ودرجة حرارته والإنتاجية محدودة بسبب تفاقم صعوبات إنتاج الأسطوانة (وهي الوعاء الأكبر أبعاداً)، إذ لم يمكن زيادة ضغط البخار أكثر من 15 بار ورفع الإنتاجية أكثر من 10 طن/سا. ولقد أمكن لاحقاً رفع المردود بتخفيض درجة حرارة خروج غازات الاحتراق اعتماداً على زيادة عدد أشواط حركة الغازات إلى ثلاثة أشواط أو أربعة.
إن الميزة الكبرى لمراجل أنابيب الماء هي أن الماء والبخار اللذين يتعرضان للضغوط العالية يتحركان في أقنية أسطوانية الشكل، صغيرة الأقطار، قادرة على تحمل الضغوط العالية، ولقد ساعد هذا الأمر على رفع مؤشرات البخار المنتج (الضغط ودرجة الحرارة) وإنتاجية المرجل الكتلية أضعافاً مضاعفة. حيث وصل ضغط البخار في المراجل المعاصرة إلى ما يزيد على 300 بار ورفع الإنتاجية الكتلية إلى 4000 طن/سا. وفي البداية كانت أقنية الماء والبخار (الأوعية) المعرضة للحرارة تتألف من عدة أسطوانات (3-9 أسطوانات)، ثم صارت تتألف من عشرات ومئات الأسطوانات الصغيرة الأقطار التي تحولت فيما بعد إلى أنابيب غليان تغلف الأسطح الداخلية لغلاف حجرة الاحتراق، أو موجودة في حزم تلامسها الغازات الساخنة الجارية ضمن مسارها.
المرجل البخاري (مكون في محرك رئيسي)
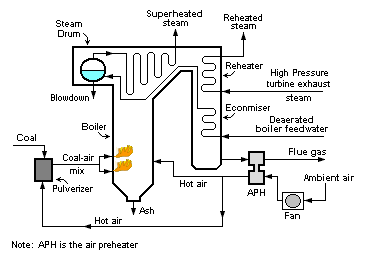
التجهيزات الأساسية للمرجل
- صمام أمان Safety valve
- Pressure measurement
- Blowdown Valves
- Main steam Stop Valve
- Feed check valves
- Fusible Plug
- Water gauge
- Low-Water Alarm
- Low Water Fuel Cut-out
- Inspector's Test Pressure Gauge Attachment
- Name Plate
- Registration Plate
- Feedwater pump
تصنيف المراجل
1ـ تصنيف المراجل حسب الوظيفة:
مراجل الطاقة: وتتميز بارتفاع إنتاج البخار الساعي وبارتفاع مؤشرات البخار المنتج، وتكون متطلبات الوثوقية والاقتصادية فيها عالية بصورة خاصة.
المراجل الصناعية: وتنتج البخار لتلبية الأغراض الصناعية في المعامل.
مراجل التدفئة: وينتج فيها البخار أو الماء الساخن لأغراض التدفئة والاستهلاك السكني.
مراجل الأغراض الخاصة: وتصمم للاستفادة من مصادر الطاقة المتجددة: مثل المصادر الثانوية الصناعية (غازات العادم الناتجة من التجهيزات الصناعية) والشمسية والكتلة الحيوية مثل فضلات المدن.
2 ـ تصنيف المراجل بحسب قيمة ضغط البخار المنتج: وهي تنتمي إلى فئة الضغط المنخفض (حتى 10 بار)، والضغط المتوسط (10-100 بار)، والمرتفع (140 بار)، والعالي (180-200 بار)، وفوق الضغط الحرج (أعلى من 225 بار).
3 ـ تصنيف المراجل بحسب الإنتاجية الكتلية: تصنف المراجل إلى مراجل صغيرة ومتوسطة وعالية الإنتاجية. ووفقاً لطريقة تحرك المياه في سطوح التبخير وجدت بالممارسة ثلاثة أصناف من المراجل هي: مراجل الدوران الطبيعي natural-circulation boilers التي يدور الماء فيها نتيجة لفرق الكثافة في عمود هبوط الماء من الأسطوانة والكثافة المتوسطة لمزيج الماء والبخار المتشكل في عمود الصعود إلى الأسطوانة، ومراجل الدوران القسري المتكرر multiple forced circulation، التي يسرّع فيها دوران الماء ومزيج البخار في الإطار الدوراني بفعل مضخة تدوير، وأخيراً مراجل الجريان المباشر once-through boilers، التي يتحرك فيها الماء والبخار في كامل مسارهما بفعل الدفع القسري لمضخة التغذية.
العمليات الإنتاجية في المراجل الحديثة
تنفذ العمليات الإتناجية الضرورية لاستمرار عمل المرجل على نحو متواصل وآلي وفقاً للشروط الفنية. ويبين الشكل (1) مكونات المخطط الإنتاجي في حال استخدام الوقود العضوي الصلب، ويحتوي المخطط على الوحدات الإنتاجية الآتية:
1- وحدة إعداد الوقود وإمداده: في حالة الوقود السائل الثقيل، يخزن الوقود بكمية مناسبة في الخزانات. وتقوم الوحدة بالعمليات الضرورية لتحقيق أفضل الشروط لإحراقه. وتتضمن مسخنات تستمد طاقتها من البخار، الذي يسخن الوقود لتخفيض لزوجته ومنع تجمده، وعادة ما تمدد أنابيب البخار محاذية أنابيب الوقود لتسخينها. وتحتوي الوحدة على مضخات خاصة لرفع ضغط الوقود، وعلى مرشحات للتنقية. ويدور الوقود في دارة مغلقة، وتراقب لزوجته واستهلاكه ودرجة حرارته.
2 ـ وحدة معالجة المياه ونظام منع الترسيب: تُعد المياه الطبيعية غير صالحة لتعويض فاقد الماء والبخار، وتجري المعالجة المسبقة لمياه التعويض عن طريق طرح الغازات المنحلة فيها بالتسخين، كما تخفض قساوة المياه وشواردها الموجبة والسالبة عموماً إلى الحدود المعتمدة في مواصفات المراجل، وتتعلق هذه الحدود بنوع المرجل وتصميمه. تجري العمليات المناسبة في داخل المرجل البخاري لطرح المتراكم من الأملاح في مياهه إبّان الاستثمار. ويعتمد نظام منع الترسيب على طرح كميات محددة من مياه الأسطوانة دورياً، بعد إضافة المواد المناسبة، ويؤدي التشغيل الصحيح لوحدة المعالجة، والمراقبة الواعية لها دوراً حاسماً في حماية المرجل وحسن عمله.
3 ـ نظام إمداد مياه التغذية: تمتزج مياه التعويض مع المياه المتكاثفة عن البخار في طريق العودة، ويتألف نظام الإمداد عادة من عدة مضخات تغذية feed pumps يوضع بعضها قيد الاحتياط، وتقوم المضخة برفع ضغط المياه إلى القيم التي تكفي للحصول على ضغط محدد عند خروج البخار من المرجل مع احتساب فواقد الضخ. ويؤدي نظام الإمداد دوراً مهماً في الحفاظ على المرجل من احتمالات ارتفاع درجة حرارة سطوح التسخين عند انقطاع إمداد المياه.
4ـ نظام إمداد الهواء وطرح نواتج الاحتراق: يحتاج احتراق الوقود في الحراقات إلى كميات مناسبة من الأكسجين الموجود في الهواء، ويتم دفع الهواء بوساطة مراوح التهوية إلى مسخن الهواء ومن ثم إلى الحراقات burners. تتوضع مروحة طرد غازات الاحتراق عادة قبل المدخنة وبعد مجمع الرماد، ويجهز المرجل بنظام خاص لجمع الرماد (أو السخام) الناتج من احتراق الوقود، والواضح أن تصميم هذا النظام مرتبط بنوع الوقود ونسبة الرماد في تركيبه، وتجري عمليات تخليص الرماد من الغازات بوسائل ميكانيكية وكهربائية.
5 ـ نظام المراقبة والقيادة والحماية والإنذار: في أثناء العمل الاعتيادي لمولد البخار تحدث تغيرات في طبيعة العمليات المؤثرة في عمله، ومن ذلك: نوع الوقود ورطوبته ودرجة حرارة مياه التغدية أو توقف إمدادها وتغير منسوب الماء في الأسطوانة، وتغير استهلاك البخار. ويقوم نظام القيادة والحماية بتحسس هذه المتغيرات عن طريق مجسات تنقل إشارات كهربائية إلى مركزمعالجة ومن ثم يعطي الحل المناسب، وتنقل الإشارات الصادرة عنه إلى أجهزة التنفيذ التي تقوم بإغلاق الصمام المناسب أو فتحه. كما تقوم أجهزة الإنذار السمعية والضوئية ببث إشارات الإنذار المناسبة لتدارك حالات الخطر الممكنة.
6ـ نظام تنظيف مجاري غازات الاحتراق: نتيجة للاستثمار المستمر واحتراق الوقود تتراكم كميات كبيرة من الرماد أو السخام ضمن حجرة الاحتراق أو على سطوح التسخين، ويؤدي ذلك إلى إضعاف انتقال الحرارة وهبوط المردود وزيادة استهلاك الطاقة في مراوح التهوية والامتصاص، ولهذه الغاية يجهز مولد البخار بنظام خاص يقوم بكسح الرماد (أو الخبث) بمساعدة البخار المنفلت أو بوسائل أخرى.
7 ـ نظام تنظيف ممرات الماء والبخار: على الرغم من المعالجة المسبقة للمياه ونظام منع الترسيب، تتراكم في حالات خاصة على سطوح أنابيب الماء والبخار طبقات صلبة من مركبات الكلسيوم والمغنيزيوم ومواد أخرى، وتؤدي هذه الطبقات إلى تخفيض معدلات انتقال الحرارة من الغازات إلى الماء والبخار الأمر الذي يؤدي إلى هبوط المردود وإلى زيادة درجة حرارة معدن سطوح التسخين (الأنابيب)، ويسرع في خروجها من الخدمة. تجري عملية تنظيف ممرات الماء بإجراءات فيزيائية وكيمياوية في أثناء الصيانة.
8 ـ نظام حركة الماء والبخار: تجري عملية توليد البخار في المراجل بثبات الضغط، وتبعاً لذلك يمكن الحصول على البخار المحمص على ثلاث مراحل: تسخين الماء المنضغط حتى الغليان تقريباً، وتوليد البخار في أنابيب التبخير evaporating tubes، وتحميص البخار الخارج من الأسطوانة حتى درجة حرارة التحميص المطلوبة في المحمّص. وقد يحتوي المرجل أحياناً على مبادل حراري إضافي يعاد فيه تحميص البخار العائد إلى المرجل بعد استهلاك حرارة التحميص.
تتوضع المبادلات الحرارية ـ سطوح التسخين ـ بترتيب يتوخى منه توفير أعلى اقتصادية ووثوقية للمرجل. ويبين الشكل (2) مسار الماء والبخار في مرجل بخاري ذي دوران طبيعي، حيث ترد مياه التغذية الموفر أولاً ومن ثم إلى الأسطوانة، فأنابيب الهبوط وأنابيب التوزيع، ثم تتوزع المياه على أنابيب الصعود إلى الأسطوانة، وتتشكل في أنابيب الصعود غيوم متكاثفة تسمى الجدران المائية water walls، ويخرج البخار المولد من أعلاها إلى المحمص.
. . . . . . . . . . . . . . . . . . . . . . . . . . . . . . . . . . . . . . . . . . . . . . . . . . . . . . . . . . . . . . . . . . . . . . . . . . . . . . . . . . . . . . . . . . . . . . . . . . . . . . . . . . . . . . . . . . . . . . . . . . . . . . . . . . . . . . . . . . . . . . . . . . . . . . . . . . . . . . . . . . . . . . . .
الأمن والسلامة
إن لاعتبارات الأمن والسلامة والوثوقية في الاستثمار أهمية خاصة في المؤسسات الصناعية التي تتضمن معدات معرضة لاحتمال حدوث الانفجار فيها، ذلك أن تلف بعض العناصر أو تضررها قد يؤدي إلى تخريب واسع وحوادث مفجعة.
وتخضع سلامة ووثوقية عمل المعدات المتأثرة بضغط داخلي فائض مثل المراجل والأنابيب والأوعية المضغوطة لقوانين مواصفات من الجهات الرسمية الصناعية والمدنية، وهي ملزِمة لجميع المؤسسات الخاصة والعامة. وتتناول هذه القوانين كل الشروط والمتطلبات الفنية والإدارية وأصول التدريب والتأهيل والعمل ومعدلات التصميم وأنواع المواد المستخدمة وطرائق التصنيع والتجميع ومراقبة نوعية المنتج والاستثمار والمراقبة والصيانة. وهناك مؤسسات تقوم بمتابعة تنفيذ هذه القواعد ومراقبتها بكامل الدقة المطلوبة، ولها الحق في منع تشغيل المعدات في حال ثبوت وجود خروق للأنطمة والمعدلات والتعليمات المرعية ووجود أخطار تهدد حياة الناس.
تصنع مراجل البخار والمياه الساخنة والأوعية والأنابيب المضغوطة وفق مخططات معتمدة ومنفذة من قبل جهات متخصصة ومؤهلة وفقاً للتعليمات المعتمدة. ويجهز المرجل عادة بالمعدات التي تضمن السلامة والحماية، ومنها صمامات أمان تقوم بإغلاق البخار من المرجل عند تجاوز الضغط 10% من قيمته النظامية. وتجهز المراجل العصرية بدرجات دقة متفاوتة من أجهزة حماية البيئة، تضمن معالجة غازات الاحتراق بما يحقق فصل الغازات الضارة مثل غاز الفحم وأكسيد الكبريت والمواد المشعة والحد من أضرارها.
مبادئ تصميم المراجل
يتوخى في تصميم المراجل تحقيق مستويات الوثوقية والاقتصادية والسلامة المناسبة. وهناك عدد من الاعتبارات الأخرى المهمة مثل: سهولة التصنيع والصيانة والفك والاستثمار عامة. ولتصميم المرجل جانبان إنشائي وحراري يمكن للمصمم من خلالهما تحسين أدائه.
1- الجانب الإنشائي: تعد الكرة الشكل الأمثل للأوعية المضغوطة وتليها الأسطوانة، ولكن الأسطوانة أكثر قابلية للتصنيع والاستخدام في المبادلات الحرارية. وتتناسب سماكة الأسطوانة طرداً مع قطرها وضغط السائل فيها. وينجم عن ذلك أن الأسطوانات الأقل قطراً أعلى قدرة على مقاومة الضغط، وتستخدم الأسطوانة على نطاق واسع في المراجل على شكل أنابيب طويلة متعددة الالتواءات أو أوعية أسطوانية ذات سطوح جانبية محدبة.
تنخفض مقاومة المعادن بشدة مع ارتفاع درجة حرارتها، وتُختار في تصميم المراجل أنواع الفولاذ المقاومة في درجات الحرارة العالية، وتراعى أيضاً مسائل التمدد الحراري بين أجزاء المرجل، كما تراعى ظاهرة الزحف الحراري، وتُدرس التباينات في متانة مختلف الأنابيب والمقاطع الناجمة عن الأوضاع الحرارية والهدرولية الخاصة.
2- الجانب الحراري: تنخفض درجة حرارة الغازات لدى ملامستها سطوح التسخين الموجودة في مسار الغازات، بدءاً من القيمة العالية في حجرة الاحتراق حتى 150 درجة مئوية تقريباً عند خروجها من المرجل، ويكون الفرق بين درجة حرارة الغازات من جهة والماء والبخار من جهة ثانية كبيراً في حجرة الاحتراق، وتنخفض هذه الكمية باستمرار مع انخفاض الفرق بين درجات حرارة الغازات، ويستنتج من ذلك أن استهلاك المعدن على إنشاء سطوح التسخين بهدف رفع المردود وخفض استهلاك الوقود يكون ناجعاً في حجرة الاحتراق نتيجة الفرق الكبير في درجات الحرارة بين الغازات ومزيج البخار مع الماء، وتقل أهمية إضافة سطوح تسخين جديدة كلما تبردت الغازات، ويصبح جني الحرارة من الغازات أعلى تكلفة وغير اقتصادي.
استثمار المراجل البخارية
يفهم الاستثمار على أنه تنظيم عمل المراجل على نحو آمن طويل الأمد وبأعلى اقتصادية عند إنتاج البخار المخطط له، والذي يتغير عادة تغيراً كبيراً بين ساعات الذروة وساعات الحضيض فيه.
تستخدم في الاستثمار المعاصر نظم المعلوماتية مع أجهزة التحكم التي تقوم بإدارة عمل المرجل آلياً، بما يحقق متطلبات الاستثمار المذكورة، وتوضع لذلك خريطة الأنظمة، استناداً إلى تجارب الاستلام وخبرة المعمل الصانع. في الخريطة تعطى مؤشرات البخار والماء وغازات الاحتراق والهواء للإنتاجية الاسمية والأصغرية والأعظمية والانتقالية وانحرافات المؤشرات الحدية.
تقدر وثوقية المرجل بعدد من المؤشرات، منها مُعامل استخدام وقت العمل، وهو نسبة عدد ساعات عمل المرجل الفعلية إلى عدد الساعات التقويمية الفترة نفسها، ويستخدم أيضاً مفهوم معامل الجاهزية، وهو يمثل نسبة مجموع ساعات العمل الفعلية والساعات التي يكون فيها المرجل جاهزاً للعمل إلى مجموع الساعات التقويمية الفترة نفسها. ويكون المرجل في إحدى الحالات الثلاث الآتية: العمل، الاحتياط، الصيانة. تعدّ عملية تشغيل المرجل (بدءاً من الحالة الباردة الاعتيادية) من أكثر العمليات التقنية تعقيداً ومسؤولية، وتحدد وثائق المرجل أدق التفاصيل عن الإجراءات المطلوبة لها، وهي متعلقة بتصميم المرجل ومؤشراته، وتراعى فيها مسألة عدم تجاوز معدلات تسخين (سرعة تسخين) معدن سطوح التسخين، بحيث تظل ضمن الحدود المسموح بها عند الإيقاد والتسخين، ويضمن أيضاً عدم تجاوز درجة الحرارة المسموح بها. وعلى العموم تعد العمليات الانتقالية المرتبطة بالتحميل والإيقاف عن العمل مماثلة في أهميتها ومسؤوليتها لعملية التشغيل وتجري أيضاً وفق شروط فنية محددة، ومن قبل أخصائيين مؤهلين.
قوة تحمل الغلايات
من الضروري أن تكون الغلايات قوية بدرجة كافية لتحمل الضغوط العالية بداخلها دون أن تنفجر. ولذلك تُصمم بعناية تامة ويتم اختبارها قبل استعمالها.
ويقاس الضغط داخل الغلاية بالكيلوجرام لكل سنتيمتر مربع، (كجم/سم²). ويكتب على كل غلاية مقدار الضغط الذي يمكن أن تتحمله مع توافر قدر من الأمان للاستخدام، ويركب على كل غلاية أيضًا مقياس يوضِّح مقدار الضغط بداخلها. ومن الضروري أن يكون لكل غلاية صمام للأمان طبقًا للمواصفات القياسية. فعندما يصل الضغط داخل الغلاية نقطة خطيرة، يمر البخار إلى الخارج فاتحًا صمام الأمان. انظر: صمام الأمان. وتعمل الغلايات المُستخدمة في تدفئة المنازل عند ضغط يتراوح بين 0,7كجم/سم² و1كجم/سم²، بينما تعمل غلايات محطات التوليد الصغيرة عند ضغط يتراوح بين 7كجم/سم² و17كجم/سم². وتعمل بعض الغلايات في محطات القدرة الكهربائية عند ضغط يصل إلى 240كجم/سم². أحجام الغلايات. تصل الغلايات الموجودة في محطات الطاقة الكهربائية إلى ارتفاع أعلى من مبنى مكوّن من عشرة طوابق، وربما تنتج أكثر من 70,000 كجم من البخار في الساعة الواحدة. ومن الضروري أن يتم إحراق كمية من الفحم الحجري تكفي لملء عربة سكة حديد كل ساعة، وذلك لإنتاج هذه الكمية من البخار.
معالجة مياه الغلايات
لا يمكن استخدام مياه الصنابير أو الآبار أو الأنهار في غلايات الضغط العالي لاحتوائها على شوائب تسبب تآكل الغلاية وتؤدي إلى ضعفها. وتعمل الشوائب الأخرى علي تكوّن طبقة من الرقائق الصلبة على السطح الداخلي لأنابيب الغلاية. وتؤدّي هذه الرقائق إلى خفض التوصيل الحراري خلال الأنابيب، وبالإضافة إلى ذلك يصبح معدن الأنبوب حارًا وساخنًا أكثر مما ينبغي. ولا بد من توخي الحذر والحيطة لإزالة الهواء والمواد الأخرى الذائبة من الماء الداخل إلى الغلاية. وتضاف مواد معينة للماء تتفاعل مع المواد الموجودة في الماء بالفعل وذلك لتمنع تكوّن هذه الرقائق الصلبة. انظر: إزالة عسر الماء.
انظر أيضاً
- Glossary of boiler terminology
- Boiler – colloquial name for a hot water heater (in hydronics)
- Steam generator (nuclear power) – a heat exchanger in a pressurized water reactor -equipped nuclear power plant
- Steam generator (railroad) – a device used in trains to provide heat to passenger cars